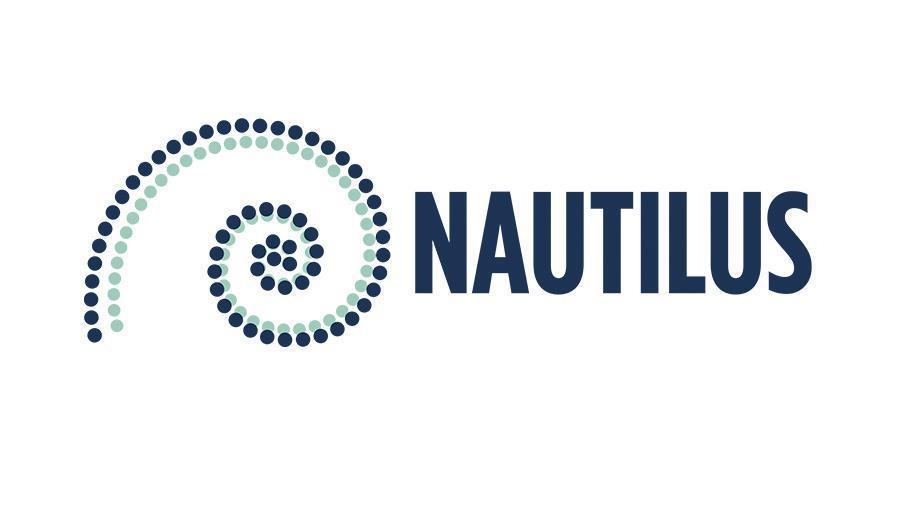
O Porriño, 16 de noviembre de 2021.- La iniciativa NAUTILUS está enmarcada en el programa de ayudas para la creación y puesta en marcha de unidades de investigación, co-financiada por la Xunta de Galicia a través de GAIN y cuenta con el apoyo de la Consellería de Economía, - Empresa e Innovación y por fondos FEDER.
La unidad mixta entre NAVANTIA y AIMEN se constituyó con la finalidad de desarrollar nuevos materiales y tecnologías de fabricación con aplicación en la industria naval militar.
Las líneas de trabajo propuestas presentan dos objetivos principales:
- El desarrollo de nuevos procesos de fabricación de sistemas automatizados para las primeras fases de fabricación del buque.
- El desarrollo de productos de mayor valor añadido, proponiendo nuevas soluciones en el área de los materiales.
NAUTILUS plantea seis líneas de trabajo, en alguna de las cuales se desarrollan en paralelo sublíneas adicionales. A continuación, se presentan los principales avances conseguidos en la anualidad 2021:
- Línea 1A – Celda prototipo para el montaje y punteo de refuerzos en previas y soportes en fase de pre-armamento. Se ha procedido al desarrollo de un nuevo demostrador para el montaje y soldadura de soportes (con metopas). Dicho demostrador ha supuesto el desarrollo y validación de los siguientes sistemas: a) Sistema de localización de probeta; b) Sistema de soldadura; c) Sistema de colocación de soportes; d) Desarrollo de un entorno software CAD/CAM que permite obtener las trayectorias offline de los robots de montaje y soldadura, partiendo del CAD del ensamblaje y la parametrización del proceso. Asimismo, se ha procedido al desarrollo de la arquitectura de control de la celda, así como de otras actividades necesarias para la realización del demostrador, a saber: programación PLC, definición de parámetros óptimos de soldeo, diseño y fabricación de alimentador/almacenador de soportes.
- Línea 1B – Desarrollo entorno colaborativo. Se ha finalizado el desarrollo de las tecnologías propuestas en la línea, centradas en seguridad, interacción y realidad aumentada. Así, por un lado, se ha realizado una demostración de fabricación en las instalaciones de Navantia con soporte de realidad aumentada en la fase de habilitación naval, mediante la utilización del sistema de proyección para asistir a los operarios en la soldadura de componentes para la instalación de paneles de aislamiento, eliminando la fase de marcado y asegurando la correcta distribución geométrica. Por otro lado, y ya en los laboratorios de AIMEN, se ha finalizado la integración de las tecnologías que componen el sistema robotizado para uso en espacio compartido con trabajadores, permitiendo el uso de un robot industrial en modo colaborativo mediante guiado manual. Para la demostración, se ha implementado una aplicación de soporte a manipulación para la instalación de refuerzos durante la fabricación de previas, con un sistema de seguridad que permite al robot operar tanto en modo manual como automático, este último sin necesidad de rearme y sin la intervención de los trabajadores. Como complemento, se han unido el sistema de proyección a la celda robotizada para facilitar la colocación de los elementos, eliminado la fase de medición y marcado.
- Línea 2 – Soldadura láser híbrido: Se han realizado nuevas uniones soldadas en materiales de pequeño espesor a fin de establecer los parámetros óptimos de soldeo con el nuevo material base, de composición ajustada a las necesidades de Navantia en pequeños espesores. Se han efectuado pruebas con y sin precalentamiento y empleando un nuevo material de aporte diferente, con el objetivo de determinar su influencia en la resistencia a impacto. En las pruebas se ha tratado de maximizar la velocidad del proceso de soldeo, a fin de incrementar al máximo la productividad, manteniendo el cumplimiento con los requisitos de calidad establecidos por la normativa aplicable.
- Línea 3 – Conformado automático de chapas por inducción. Se han finalizado la puesta a punto del sistema automático de conformado (ajuste de los servomotores de la Cama ajustable multipunto, integración de seguridades de celda, integración de sensor láser para medida, comunicación de todos los elementos), y la programación del robot para la ejecución de las trayectorias de conformado. Asimismo, se ha continuado trabajando en el desarrollo del sistema machine learning y en los modelos de simulación. Por último, se ha trabajado en la optimización del inductor electromagnético para mejorar la eficiencia del proceso.
- Línea 4 – Soluciones para construcción/reparación naval basadas en composites. Se ha procedido a una optimización del proceso de fabricación y caracterización del abanico de materiales ignífugos seleccionados en la anterior anualidad. Las seis combinaciones de materiales seleccionadas para el demostrador (puerta) se han enviado a un centro acreditado para la realización de los ensayos experimentales de resistencia a fuego. Con los resultados obtenidos, se ha seleccionado la combinación óptima de cara a la fabricación de una puerta a escala real que será ensayada a fuego en centro acreditado.
- Línea 5 – Soluciones ligeras para blindaje. Se ha procedido a la fabricación de paneles, con nuevos materiales, para los ensayos balísticos en centro acreditado. En paralelo, se ha estado trabajando en las posibles estrategias de sujeción del panel de material compuesto en el forro reforzado seleccionado como caso de estudio.
- Línea 6 – Soluciones para protección catódica de buques y estructuras offshore. Se ha finalizado el proceso de adjudicación del material para la construcción del nuevo prototipo de cabinet portátil para la protección catódica. Dicho cabinet se someterá a pruebas de validación en las instalaciones de Navantia-Ferrol con el objetivo de implantar la solución alcanzada en las mismas. Asimismo, se ha presentado un trabajo de divulgación de resultados en el Congreso Europeo Eurocorr 2021, celebrado del 20 al 24 de septiembre de 2021 de forma virtual, y con título título: Cathodic Protection Systems on Warships. Correspondiente al panel WP9&16: Cathodic Protection in Marine Environment.
Financiación
La iniciativa NAUTILUS enmarcada en el programa de ayudas para la creación y puesta en marcha de unidades mixtas de investigación, está financiada por la Xunta de Galicia a través de la Axencia Galega de Innovación (GAIN) y cuenta con el apoyo de la Consellería de Economía, Empresa e Innovación. A su vez, está cofinanciada con cargo a Fondos FEDER en el marco del eje 1 del programa operativo Feder Galicia 2014-2020. (Ref. IN853A 2018/03).